Simple New Process Stores CO2 in Concrete While Maintaining Strength
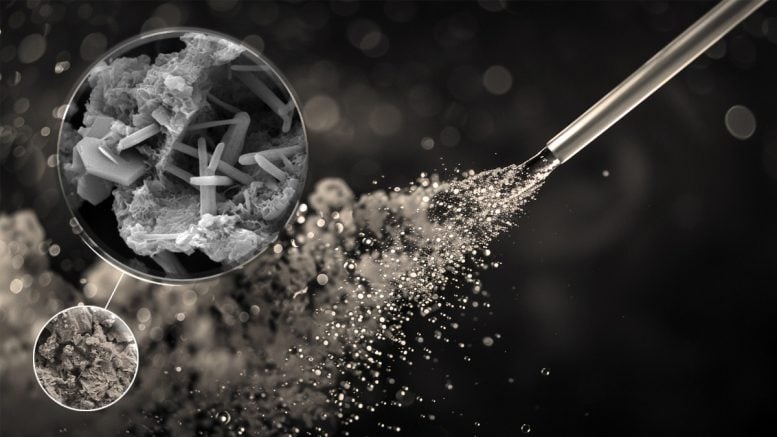

A team at Northwestern University has developed a new concrete manufacturing process using carbonated water to sequester carbon dioxide, achieving a CO2 capture efficiency of up to 45%. This method not only helps reduce atmospheric CO2 but also produces concrete with enhanced strength and durability, making it a promising solution for lowering emissions from the cement and concrete industries. Credit: Alessandro Rotta Loria/Northwestern University
Carbonated concrete could help reduce emissions associated with cement production.
By using a carbonated — rather than a still — water-based solution during the concrete manufacturing process, a Northwestern University-led team of engineers has discovered a new way to store carbon dioxide (CO2) in the ubiquitous construction material.
Not only could the new process help sequester CO2 from the ever-warming atmosphere, it also results in concrete with uncompromised strength and durability.
In laboratory experiments, the process achieved a CO2 sequestration efficiency of up to 45%, meaning that nearly half of the CO2 injected during concrete manufacturing was captured and stored. The researchers hope their new process could help offset CO2 emissions from the cement and concrete industries, which are responsible for 8% of global greenhouse gas emissions.
The study was published in Communications Materials, a journal published by Nature Portfolio.
“The cement and concrete industries significantly contribute to human-caused CO2 emissions,” said Northwestern’s Alessandro Rotta Loria, who led the study. “We are trying to develop approaches that lower CO2 emissions associated with those industries and, eventually, could turn cement and concrete into massive ‘carbon sinks.’ We are not there yet, but we now have a new method to reuse some of the CO2 emitted as a result of concrete manufacturing in this very same material. And our solution is so simple technologically that it should be relatively easy for industry to implement.”
“More interestingly, this approach to accelerate and accentuate the carbonation of cement-based materials provides an opportunity to engineer new clinker-based products where CO2 becomes a key ingredient,” said study coauthor Davide Zampini, vice president of global research and development at CEMEX.
Rotta Loria is the Louis Berger Assistant Professor of Civil and Environmental Engineering at Northwestern’s McCormick School of Engineering. The study was a collaboration between Rotta Loria’s laboratory and CEMEX, a global building materials company dedicated to sustainable construction.
Limitations of previous processes
A non-negotiable part of infrastructure, concrete is one of the world’s most consumed materials — second only to water. To make concrete in its simplest form, workers combine water, fine aggregates (like sand), coarse aggregates (like gravel), and cement, which binds all the ingredients together. Since the 1970s, previous researchers have explored various ways to store CO2 inside concrete.
“The idea is that cement already reacts with CO2,” Rotta Loria explained. “That’s why concrete structures naturally absorb CO2. But, of course, the absorbed CO2 is a small fraction of the CO2 emitted from producing the cement needed to create concrete.”
Processes to store CO2 fall into one of two categories: hardened concrete carbonation or fresh concrete carbonation. In the hardened approach, solid concrete blocks are placed into chambers where CO2 gas is injected at high pressures. In the fresh version, workers inject CO2 gas into the mixture of water, cement, and aggregates while concrete is being produced.
In both approaches, some of the injected CO2 reacts with the cement to become solid calcium carbonate crystals. Both techniques, however, share deal-breaking limitations. They are hindered by low CO2 capture efficiency and high energy consumption. Even worse: The resulting concrete is often weakened, hampering its applicability.
Uncompromised strength
In Northwestern’s new approach, the researchers leveraged the fresh concrete carbonation process. But, instead of injecting CO2 while mixing all the ingredients together, they first injected CO2 gas into water mixed with a small amount of cement powder. After mixing this carbonated suspension with the rest of the cement and aggregates, they achieved a concrete that actually absorbed CO2 during its manufacturing.
“The cement suspension carbonated in our approach is a much lower viscosity fluid compared to the mix of water, cement, and aggregates that is customarily employed in present approaches to carbonate fresh concrete,” Rotta Loria said. “So, we can mix it very quickly and leverage a very fast kinetics of the chemical reactions that result in calcium carbonate minerals. The result is a concrete product with a significant concentration of calcium carbonate minerals compared to when CO2 is injected into the fresh concrete mix.”
After analyzing their carbonated concrete, Rotta Loria and his colleagues found its strength rivaled the durability of regular concrete.
“A typical limitation of carbonation approaches is that strength is often affected by the chemical reactions,” he said. “But, based on our experiments, we show the strength might actually be even higher. We still need to test this further, but, at the very least, we can say that it’s uncompromised. Because the strength is unchanged, the applications also don’t change. It could be used in beams, slabs, columns, foundations — everything we currently use concrete for.”
“The findings of this research underline that although carbonation of cement-based materials is a well-known reaction, there is still room to further optimize the CO2 uptake through a better understanding of the mechanisms tied to materials processing,” Zampini said.
Reference: “Storing CO2 while strengthening concrete by carbonating its cement in suspension” by Xiaoxu Fu, Alexandre Guerini, Davide Zampini and Alessandro F. Rotta Loria, 26 June 2024, Communications Materials.
DOI: 10.1038/s43246-024-00546-9
The study was supported by CEMEX Innovation Holding Ltd.