A Breakthrough in Efficiency and Cost – World Pakistan

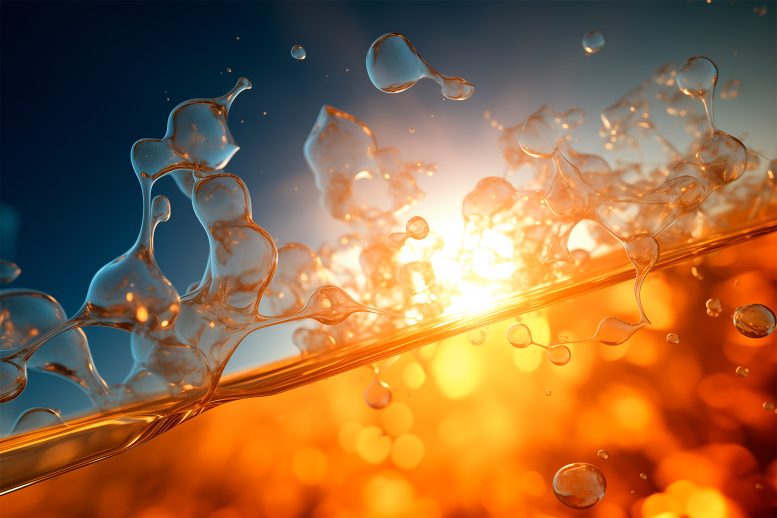
Gas separation is crucial across many industries but often involves energy-intensive processes, such as cooling gases to liquefy and then separate them based on their evaporation temperatures. However, Professor Wei Zhang and his team at the University of Colorado Boulder have developed a new type of porous material that is flexible, sustainable, and energy-efficient. This material can adjust its pore sizes at different temperatures to selectively allow certain gases to pass through, potentially revolutionizing the way gases are separated and reducing the overall energy required for these processes.
A new porous material allows for efficient, low-energy gas separation and is scalable for industrial use, offering a sustainable alternative to traditional methods.
Separating gases plays a crucial role in various industries, from medical applications, where nitrogen and oxygen are separated from air, to environmental processes like carbon capture, where carbon dioxide is isolated from other gases, and the purification of natural gas by removing impurities.
Separating gases, however, can be both energy-intensive and expensive. “For example, when separating oxygen and nitrogen, you need to cool the air to very low temperatures until they liquefy. Then, by slowly increasing the temperature, the gases will evaporate at different points, allowing one to become a gas again and separate out,” explains Wei Zhang, a University of Colorado Boulder professor of chemistry and chair of the Department of Chemistry. “It’s very energy intensive and costly.”
Much gas separation relies on porous materials through which gases pass and are separated. This, too, has long presented a problem, because these porous materials generally are specific to the types of gases being separated. Try sending any other types of gas through them and they don’t work.
However, in research published today in the journal Science, Zhang and his co-researchers detail a new type of porous material that can accommodate and separate many different gases and is made from common, readily available materials. Further, it combines rigidity and flexibility in a way that allows size-based gas separation to happen at a greatly decreased energy cost.
“We are trying to make technology better,” Zhang says, “and improve it in a way that’s scalable and sustainable.”
Adding flexibility
For a long time, the porous materials used in gas separation have been rigid and affinity-based—specific to the types of gases being separated. The rigidity allows the pores to be well-defined and helps direct the gases in separating, but also limits the number of gases that can pass through because of varying molecule sizes.
For several years, Zhang and his research group worked to develop a porous material that introduces an element of flexibility to a linking node in an otherwise rigid porous material. That flexibility allows the molecular linkers to oscillate, or move back and forth at a regular speed, changing the accessible pore size in the material and allowing it to be adapted to multiple gases.
“We found that at room temperature, the pore is relatively the largest and the flexible linker barely moves, so most gases can get in,” Zhang says. “When we increase the temperature from room temperature to about 50 degrees (Celsius), oscillation of the linker becomes larger, causing effective pore size to shrink, so larger gases can’t get in. If we keep increasing the temperature, more gases are turned away due to increased oscillation and further reduced pore size. Finally, at 100 degrees, only the smallest gas, hydrogen, can pass through.”
The material that Zhang and his colleagues developed is made of small organic molecules and is most analogous to zeolite, a family of porous, crystalline materials mostly comprised of silicon, aluminum, and oxygen. “It’s a porous material that has a lot of highly ordered pores,” he says. “You can picture it like a honeycomb. The bulk of it is solid organic material with these regular-sized pores that line up and form channels.”
The researchers used a fairly new type of dynamic covalent chemistry that focuses on the boron-oxygen bond. Using a boron atom with four oxygen atoms around it, they took advantage of the reversibility of the bond between the boron and oxygen, which can break and reform again and again, thus enabling self-correcting, error-proof behavior and leading to the formation of structurally ordered frameworks.
“We wanted to build something with tunability, with responsiveness, with adaptability, and we thought the boron-oxygen bond could be a good component to integrate into the framework we were developing, because of its reversibility and flexibility,” Zhang says.
Sustainable solutions
Developing this new porous material did take time, Zhang says: “Making the material is easy and simple. The difficulty was at the very beginning, when we first obtained the material and needed to understand or elucidate its structure—how the bonds form, how angles form within this material, is it two-dimensional or three-dimensional. We had some challenges because the data looked promising, we just didn’t know how to explain it. It showed certain peaks (x-ray diffraction), but we could not immediately figure out what kind of structure those peaks corresponded to.”
So, he and his research colleagues took a step back, which can be an important but little-discussed part of the scientific process. They focused on the small-molecule model system containing the same reactive sites as those in their material to understand how molecular building blocks packed in a solid state, and that helped explain the data.
Zhang adds that he and his co-researchers considered scalability in developing this material, since its potential industrial uses would require large amounts, “and we believe this method is highly scalable. The building blocks are commercially available and not expensive, so it could be adopted by industry when the time is right.”
They have applied for a patent on the material and are continuing the research with other building block materials to learn the substrate scope of this approach. Zhang also says he sees potential to partner with engineering researchers to integrate the material into membrane-based applications.
“Membrane separations generally require much less energy, so in the long term they could be more sustainable solutions,” Zhang says. “Our goal is to improve technology to meet industry needs in sustainable ways.”
Reference: “Molecular recognition with resolution below 0.2 angstroms through thermoregulatory oscillations in covalent organic frameworks” by Yiming Hu, Bratin Sengupta, Hai Long, Lacey J. Wayment, Richard Ciora, Yinghua Jin, Jingyi Wu, Zepeng Lei, Kaleb Friedman, Hongxuan Chen, Miao Yu and Wei Zhang, 27 June 2024, Science.
DOI: 10.1126/science.adj8791